Surface finishing is a series of industrial processes that alter the surface of a manufactured product to achieve a certain mechanical capacity. Hundreds of thousands of tons of steel products are galvanized each year around the world.
So good surface treatment for steel components is much related to a good mechanical capacity of components.It is of great significance to choose an optimum surface treatment for construction steel.
Next, let me introduce several common surface treatment methods for construction steel respectively.
WHY SURFACE TREATMENT IS REQUIRED FOR CONSTRUCTION STEEL?
In order to prevent corrosion or merely improve appearance, engineers often choose surface treatment which is applied to the surface of a steel material for adding functions such as rust ,wear and tear resistance.
Additionally, some types of surface treatment can also enhance construction steel capacity, which increases the overall functionality of the steel component.
As you know, whatever the reason is, surface treatment is a crucial finishing process in production of metal components.
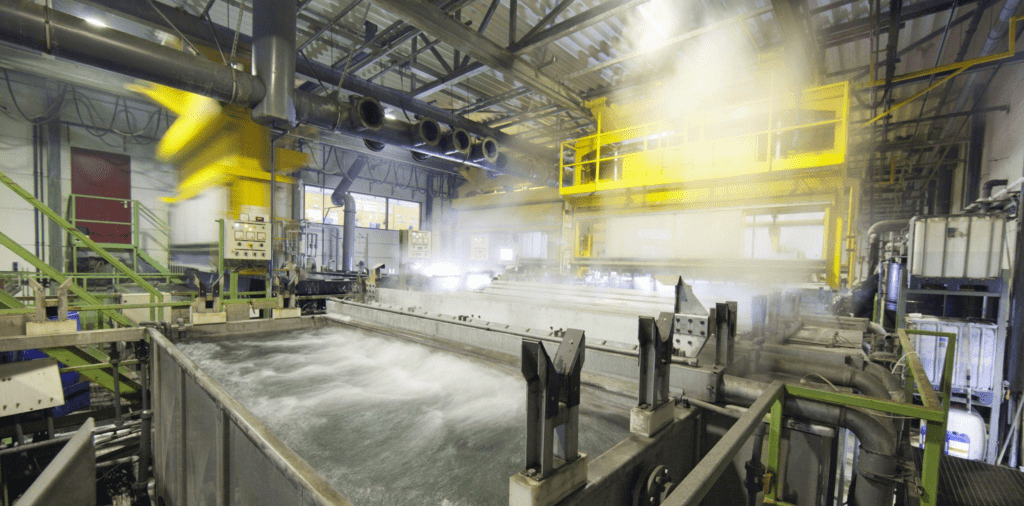
1、 Electro galvanized method
Galvanizing, also known as cold galvanizing, is the process of forming a uniform, dense, and well-bonded zinc coating on the surface of the workpiece using the principle of electrolysis. It is also the most common surface treatment for construction steel, components for products like temporary fences and scaffoldings.
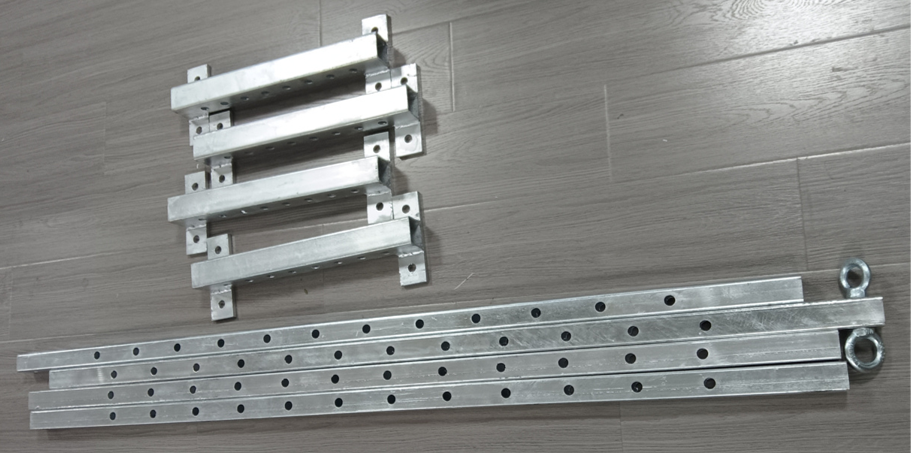
BASIC INFORMATION
- Thickness: 5-30μm
- Zinc content: 15g/㎡-200g/㎡
- Life span: 2-5 years
- Appearance: smooth, bright, flat
- Application: Used for small parts or components that require precise coatings, such as fasteners or electronic components.

Production process
Degreasing – Cleaning – Pickling and rust removal – Cleaning – Galvanizing – Cleaning – Polishing – Cleaning – Passivation – Hot water rinsing – Drying
2、 Hot-dipped galvanized method
Hot-dip galvanizing is one of the most effective ways to delay the environmental corrosion of steel materials and can also apply for temporary fences and scaffoldings. . It involves immersing cleaned and activated steel products in molten zinc, allowing a good adhesion of zinc alloy coating to be deposited on the surface of the steel products through the reaction and diffusion between iron and zinc.
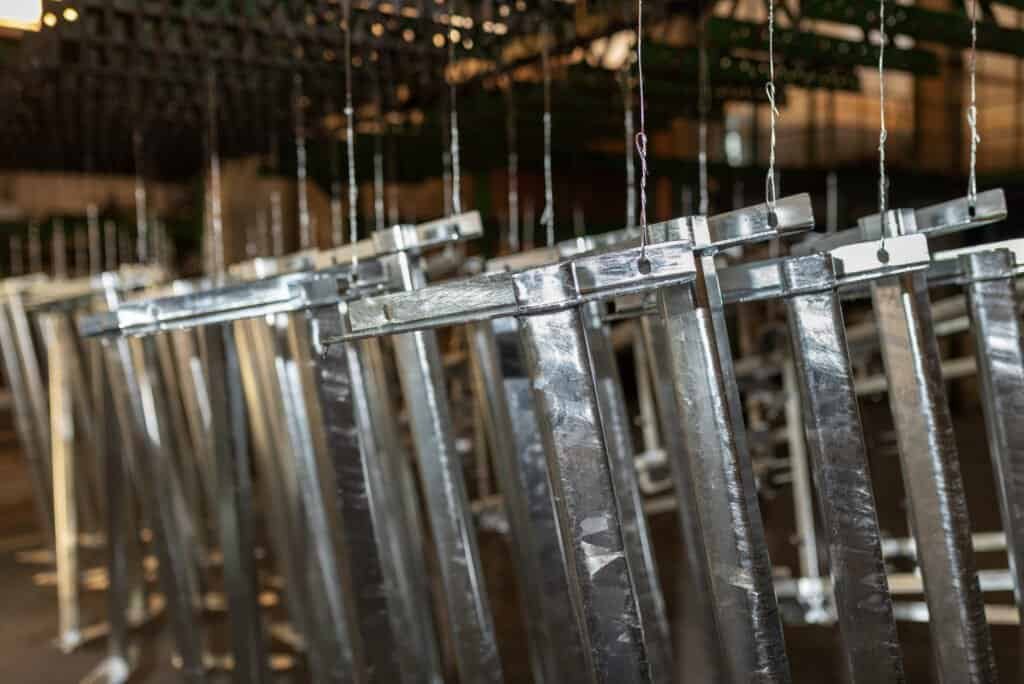
Basic information
- Thickness:45-200μm
- Zinc content: 50g/㎡-600g/㎡
- Life span: more than 20 years
- Appearance: dark, a little rough
- Application: Power transmission towers, communication towers, railway, highway protection, street lighting poles, etc.
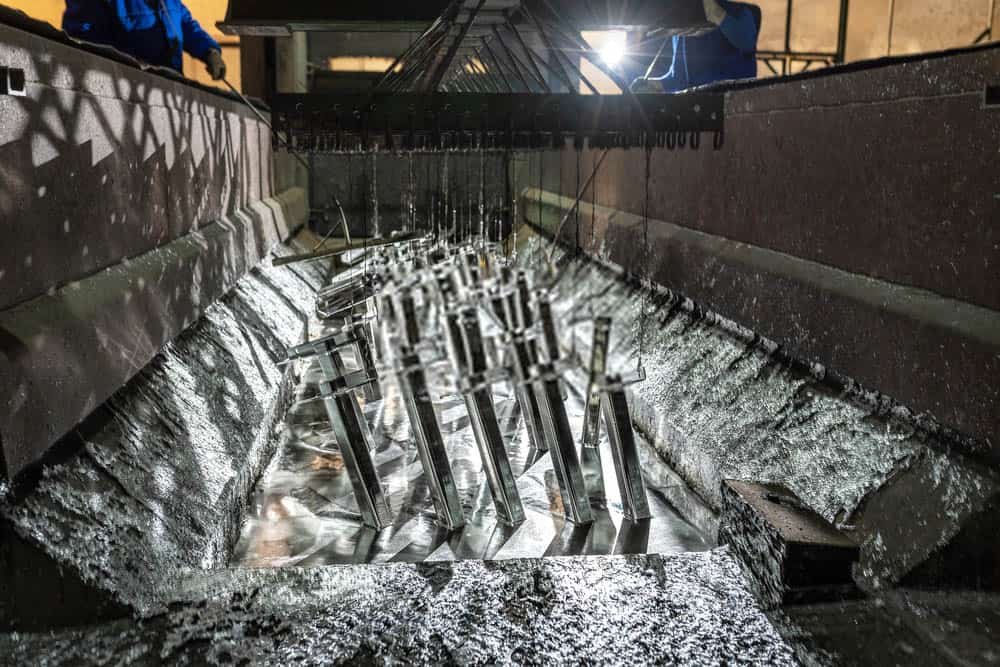
Production process
Degreasing (if necessary) – Pickling and passivation – Cleaning – Pre-plating – Drying – Plating – Water cooling – Passivation – Cleaning – Polishing
3、 Shot blast
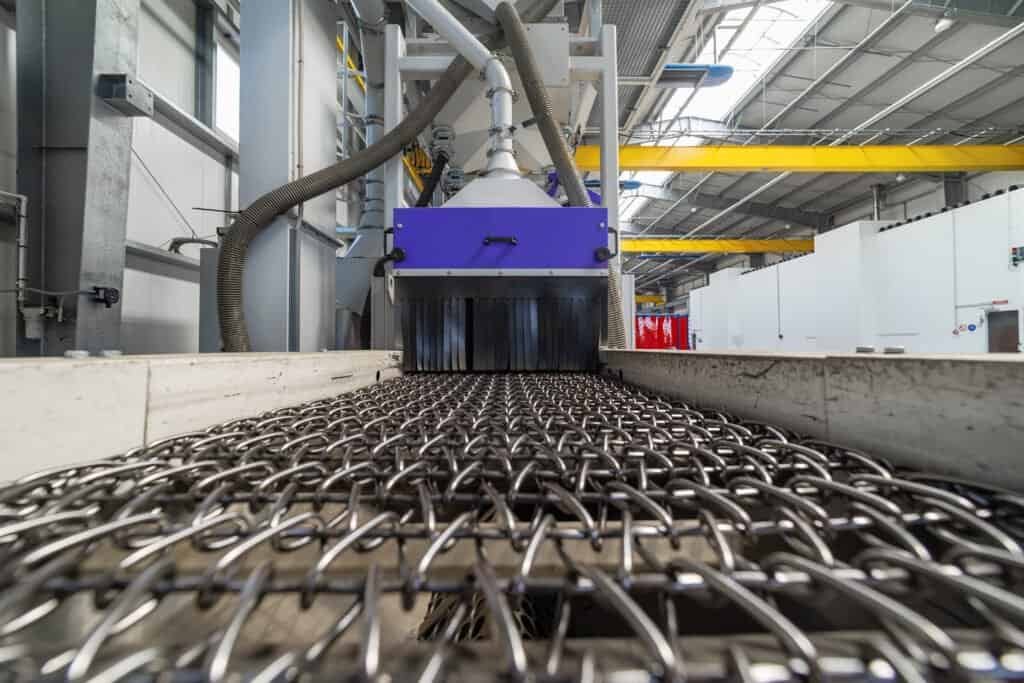
Processing principle
The processing principle of shot blasting is to use an electric motor to drive the impeller body to rotate (direct drive or V-belt drive), and by the action of centrifugal force, the shot with a diameter of about 0.2 to 3.0 is thrown towards the surface of the workpiece, so that the surface of the workpiece reaches a certain roughness, making the workpiece more beautiful, or changing the welding tensile stress of the workpiece into compressive stress, improving the service life of the workpiece.
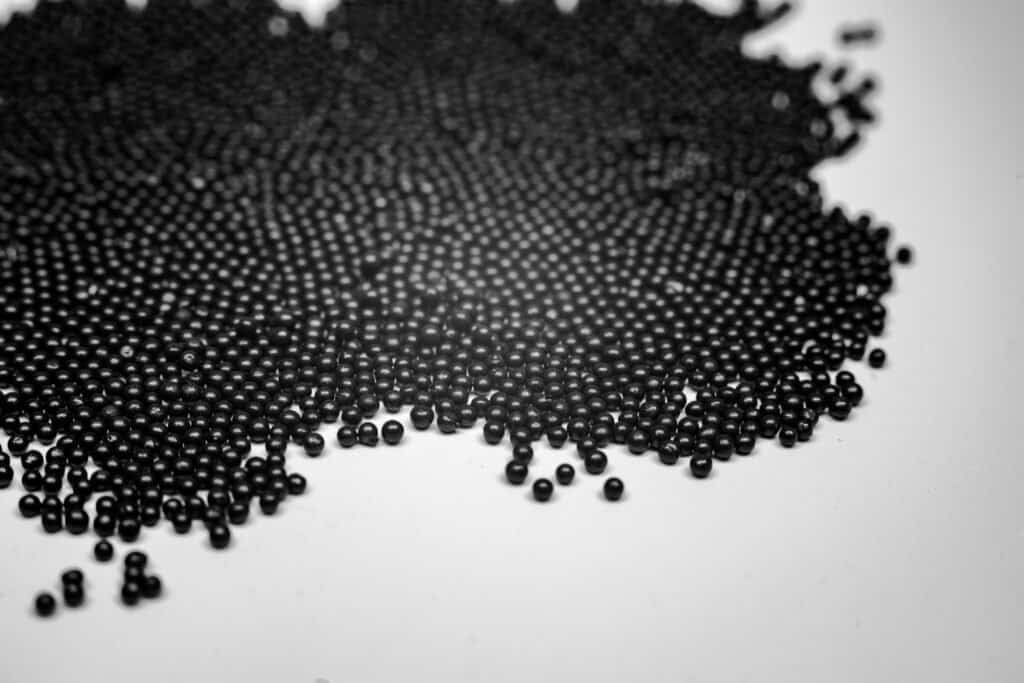
COMMON SHOT BLASTING MATERIALS
steel shot, aluminum shot, ceramic micro powder, steel sand, walnut sand, corn cob, glass beads, resin sand, plastic sand, etc.
Advantages
- Enhance the fatigue fracture resistance of materials/parts
- Prevent fatigue failure, plastic deformation and brittle fracture
- Improve fatigue life
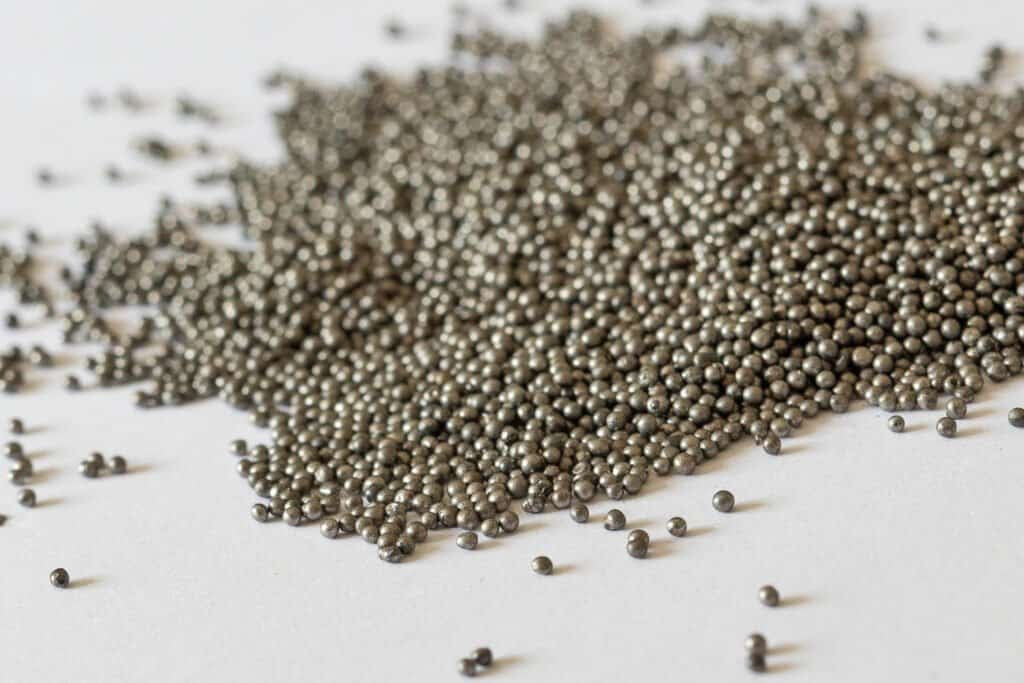
4、Powder coated method
Powder coating is a process in which plastic powder is charged through high-voltage electrostatic equipment, and under the action of the electric field, the coating is sprayed onto the surface of the workpiece. This method is often applied in Canada Temporary Fences.
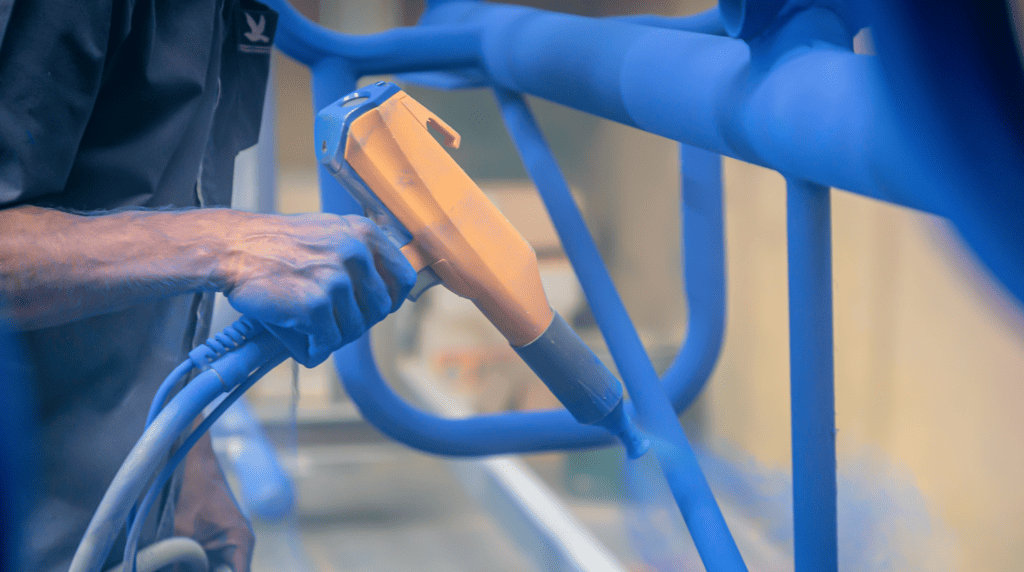
Advantages
- Atomization is sufficient, and the appearance of the coated film is good.
- High paint utilization rate: Not only is the adhesion rate high, but the paint is evenly distributed over the entire surface, with a paint utilization rate of over 80%, saving paint.
- Less paint mist dispersion: The dispersion of powder mist is much less, improving the working environment conditions and benefiting the health of workers.
- High painting production efficiency: Suitable for automated mass production.
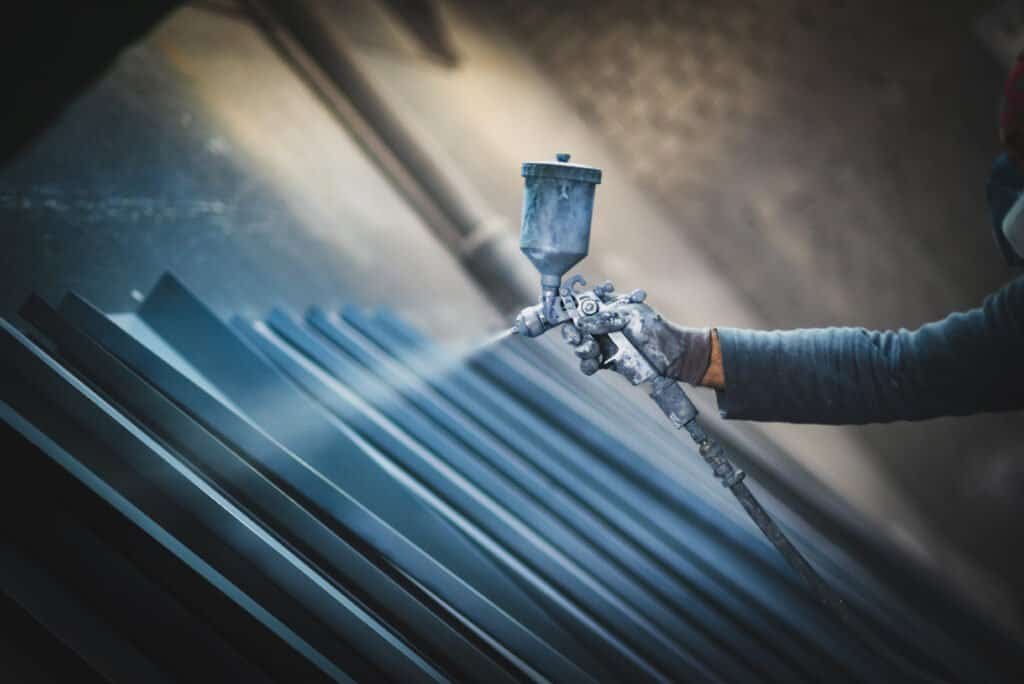
Conclusion
Now that you have learned about the most common methods of surface treatment, it can be quite easy for you to choose the right method.
When you buy any steel product, whether it be scaffolding, edge protection system, or temporary fence, make sure your product has high-quality surface treatment.
If you are looking to buy scaffolding, edge protection systems, or temporary fences with better surface treatment, contact us now.